Overview
of Six Sigma
By
P J Swamy
Dinfoka Consulting Group , Mumbai
Introduction
With
the opening up of the Indian Industry to International competition,
the pressure on Indian Industry to match international norms as
regards quality and value addition is mounting day by day.Gone
are the day’s when the industry could provide for and get
okayed for material wastages as high as 20% and rejections at
5-10%. The overall efficiency in terms rework and scrap is several
layers below world class level.
Simultaneously , the domestic market is getting saturated and
exports is the only solution for survival.
To meet global competition , the Indian Industry need to adapt
breakthrough strategies that will help reduce rejection and eliminate
waste.Six Sigma is one such proven strategy that has done wonders
in several organizations by adding millions of dollars to the
bottom line. Indian Industry should take advantage of this.
What
is Six Sigma
At superficial level Six Sigma consists of two fairly familiar
words : Six and &Sigma
The Greek letter SIGMA is a mathematical term that simply represents
a measure of variation, the distribution or spread around the
mean or average of any process or procedure in manufacturing,
engineering, services or transactions. It is represented by symbol
?
Standard Deviation
Standard deviation or Sigma is unique to a process at a given
level . If the process is normal , then it follows what is known
as Gaussian distribution
Process Width
A process has its own spread or width. The process does not understand
tolerance , it only operates at its own variation .
This is called VOP or Voice of the Process in Six Sigma
Relation
between process variation ? and process width
For example , if a process has a standard deviation of ? , and
if the process is normal,
then the process width is equal to +/- 3 ? over mean or the process
spread is equal to 6 ?
A
process is an activity that converts an input into output .The
requirements of the out put are given by customer .The variation
in the out put is governed by process.
Customer
Standard or Specification
The Customer usually provides a specification that has a mean
or target value. He also provides limits to account for process
variation-
LSL- Lower Specification Limit and
USL- Upper Specification Limit
Specification
Range (R)
The specification range is
USL-LSL
Process Capability & Process
Sigma Level
Process Capability(Cp)
This
is a measure of how capable the process is as compared to specification
range
= Specification Range / Process Width
One
Sigma Process
1 sigma process is one that has range equal to +/-1 ? from the
mean
1 sigma process is same as the one with process capability 0.33
In a 1 Sigma process, 31.73 % of the out put lies out of spec.
At this level of quality no company survive.
2
Sigma Process
A 2 sigma process is one that has range equal to +/-2 ? from the
mean
2 sigma process is same as the one with process capability 0.66
In a 2 Sigma process, 4.55 % of the out put lies outside the spec.
3
Sigma Process
A 3 sigma process is one that has range equal to +/-3 ? from the
mean
3 sigma process is same as the one with process capability 1.00
In a 3 Sigma process, 0.27 % of the out put lies out side the
spec.
4
Sigma Process
A 4 sigma process is one that has range equal to +/-4 ? from the
mean
4 sigma process is same as the one with process capability 1.33
In a 4 Sigma process, .0063 % of the out put lies outside the
spec.
5 Sigma Process
A 5 sigma process is one that has range equal to +/-5 ? from the
mean
5 sigma process is same as the one with process capability 1.66
In a 5 Sigma process, .000057 % of the out put lies outside the
spec.
6
Sigma Process
A 6sigma process is one that has range equal to +/-6 ? from the
mean
6 sigma process is same as the one with process capability 2.00
In a 6 Sigma process, only .0000002 % of the out put lies outside
the spec.
What
is wrong with 3 Sigma Process
Let
us see what can happen in key areas of life if things were to
be at 3 sigma level or only
1. One
Hour Of Unsafe Drinking Water Every Month
2. Two Long Or Short Landings
At Every Major Airport Each Day
3. 400 Letters Per Hour Which
Never Arrive At Their Destination
4. 500 Incorrect Surgical Operations
Each Week
5. 3,000 Newborns Accidentally
Falling From The Hands Of Nurses Or Doctors Each Year
6. 4,000 Incorrect Drug Prescriptions
Per Year
7. 22,000 Checks Deducted From
The Wrong Bank Account Each Hour
8. 32,000 missed
heartbeats per person per year
Life
with Six Sigma
13
wrong drug prescriptions per year as against 4000
10 newborns
accidentally falling from the hands of nurses or doctors each
year as against 3000
1 lost article
of mail per hour as against 400
Six
Sigma for Orgnaisational Survival
Survival
of an Organisation depends on Business Growth
Business Growth
depends on Customer Satisfaction
Customer Satisfaction
depends on Quality Price and Delivery
Quality Price
and Delivery depends on Process Capability
Process Capability
depends on Limited Variation
Limited Variation
depends on Application of Right Knowledge
Six Sigma is
the Right Knowledge which is a break through strategy
What
is a break through strategy and how do we know that Six Sigma
is a proven methodology to achieve business growth?
Breakthrough
Strategy is to ask a new set of questions -Questions that take
you out of your comfort zone.
Can you continue
to be in business when your cost of quality is as high as 25%?
Can you remain
in hotel business if the check in time takes more than five minutes?
Can you be
in business if your inventory is more than 3 days?
Will any customer
float an enquiry if you take more than a day for quotation?
It
also challenges things you have taken for granted.
10
hours tool changeover time is the minimum that one can think of
. My customers have been accepting this
for years.
In
our type of business, 20 % rework is quite common
80
% efficiency is excellent and nothing better can be done !
And
ultimately provides you with new directions to find answers.
And this is where six sigma has powerful tools
The
origin and development of Six Sigma
The
origin of six sigma
The
foundation for the development of Six Sigma concept was laid down
at Motorola in 1979 when executive Art Sundry stood up at a management
meeting and dared to say “The real problem at Motorola is
that our quality stinks!”
Art Sundry’s criticism was based on the fact the Motorola
was spending 5 to 10 % of annual revenues and sometimes even up
to 20% in correcting poor quality. This translated into a whopping
$800 to 900 million each year
Spurred
by the comment of Sundry , a Motorola executive by name Bill Smith
started a work that studied the relation between a product’s
field life and how many times it was repaired and okayed during
process before being dispatched.
Bill
Smith’s study concluded that –
If a product was found defective and corrected for some defects
during the process , other defects were bound to be missed and
found later by the customer during early use of the product. However,
if the product is made error free, then it rarely had any failures
at customers end.
This means hidden defects kill product performance.
Till
the findings of Bill Smith, all American companies believed that
it is cheaper to fix defects than make products defect free. And
once a product is inspected, it would go out defect free.
Bill’s
study had shaken this belief at Motorola and the question he put
to all was-
If
hidden defects caused a product to fail shortly after the customer
started using it , something needed to be done to improve the
process
.It
also made to rethink the trade off between cost of quality and
cost of the product .
It
is this quest to meet a make a product defect free and yet make
it cost effective that led to the birth of the Six Sigma strategy
at Motorola
This technique was first tried for the development of Bandit pager.
For a budget pegged at $10million* , 23 Motorola engineers had
come out in a record 18 months time with a pager that
Was
the cheapest in the market
Had an average life expectancy of 150 Years(No typing mistake)
and
Could be produced within seventy two minutes (again no typing
mistake for hours or days) after a sales man places an order by
computer from any of Motorola offices!
*( Motorola was losing $800million annually on cost of quality)
Motorola
had formalized the strategy by giving it a name “Six Sigma”
and in three years saved $ 2.2 billion .
By
1993 , Motorola was operating at near six sigma at all its plants
and the success of Six Sigma at Motorola spread like wild fire
and the first strategist to take quick advantage of this was Lawrence
A Bossidy of Allied Signal and the first visionary to see its
potential was Jack Welch of General Electric
The
Development of six sigma- Allied Signal
In
seven years time from 1991 to 1998 by adapting Six Sigma Strategy
Allied Signal could raise its market value from $4 billions to
$29 billions and save a whopping $2 billion dollars and this is
what Bossidy had to say at the end –
“Every
time we think we have generated the last dollar out of our business
, by using Six Sigma Strategy , we uncover new ways to harvest
cash as we reduce cycle times , lower inventories , increase out
put and reduce scrap. The outcome is better and more competitively
priced products , more satisfied customers who give us more business
– and improved cash flow.”
The test of Six Sigma - GE
At the time when Allied Signal was reaping rich rewards under
Six Sigma Strategy , General Electric was at its peak performance
under the dynamic leadership of Jack Welch. Jack Welch had guided
the growth of GE from a market value of $12 billion in 1981 to
about $280 billion in 1998.
And Jack was known for his allergy to management fads and quality
programs including TQM. He believed that they were all heavy on
slogans and light on results.
Lawrence A Bossidy was an ex GE Vice Chairman and a long time
friend of Jack. He happened to share with Jack the benefits that
Six Sigma strategy brought to Allied Signal. Welch had requested
Bossidy help assess where GE was and implement Six Sigma to make
it best in class.
In
1996 , GE was at 3 Sigma and the gap between being a three sigma
and six sigma company was costing GE an astounding 7 to 10 billion
dollars and immediately Welch saw a gold mine and proclaimed in
1996 AGM-
“Six
Sigma- GE Quality by 2000- will be the biggest , the most personally
rewarding , and , at the end , the most profitable undertaking
in our history. We have set ourselves the goal of becoming , by
year 2000, a six sigma quality company , which means a company
that produces virtually defect free products , services and transactions.”
Due
to the six sigma strategy GE could generate additional profits
of $ 250 millions in 1997 itself- in just one year time.
Six
Sigma is not just a Quality Tool...
Six
sigma is a Philosophy-
A
philosophy which believes that” whatever the halo of esteem
a company has in the eyes of the society, no company is truly
excellent unless it makes profits”
A
philosophy which believes that the possibility of making mistakes
and creating waste is equally in both hard and soft areas of organization
A
philosophy which believes that the yard stick to assess errors
should be common to all areas –manufacturing , purchase
accounts etc (Six Sigma has a uniform standard measuring scale
for manufacturing and non manufacturing – this is called
DPMO- Defects Per Million Objectives.)
A
philosophy which truly believes in customer as god and helps organisations
listen to his voice- VOC. Voice Of the Customer-is a major philosophy
on which six sigma concept is built.
Six
Sigma is a Vision
A
vision which envisages continuous and drastic changes in the customer
improvements in reduction in defects- the vision to achieve a
defect level of 3.4 DPMO.
Six
sigma is a vehicle for customer focus
Six
sigma is a vehicle which drives you towards your customer satisfaction
and delight by synchronizing the activities of entire organisation
to that of customer needs.
Six
sigma is an aggressive goal
Unlike
kaizen and other incremental improvement techniques , Six Sigma
is very aggressive goal that aims at not incremental improvements
but aggressive goals-
Reduce
mould change over time by ½
Improve profitability
by 10 times
Reduce rejection
level by ½
It
is a management system
It
is a management system that has absorbed and aligned several management
techniques into one comprehensive management system called Six
Sigma Management System.
Six
Sigma is a strategy that embraces loss function philosophy as
against goal post mentality
Goal
Post Mentality
In
a badminton game, when your opponent misses to return the ball,
what are the possible out comes ?
If
the ball hits the ground within the boundary, you gain a point
If
the ball hits the boundary or anywhere outside , you lose a point.
This
is called goal post mentality
Loss
Function
Goal
post mentality which is applicable in sports is not at all applicable
in process.
The
loss function does not treat all parts within spec as of equal
quality. This is called loss function mentality as propounded
by Taguchi.
Loss
function describes the loss that occurs when a process does not
produce a product that meets target value.
Loss
is minimised when there is no variation and the best response
is achieved in all areas of product design.
Loss
function
L=k(y-m)2
Where
K= loss factor
Y= the value of the parameter that is under assessment
m= mean value of the process
Six
Sigma is a universal capability measuring scale
Six
Sigma – A universal Scale which can answer the following
questions :
The
ID of 100 steel tubes was inspected with go –no go gauge
and found 10 not ok.
What is the process capability?
95
invoices have been made and out of them 8 are found defective
What is the process capability?
The
telephone operator received 85 phone calls and diverted 6 calls
to a wrong extension
What is the process capability?
In
hotel , every day morning for breakfast 5 out of 100 times , you
have been served with wrong dish.
What is the process capability?
An
airline boasts of maximum 10 minutes time lapse from the time
the plane lands to the time the luggage starts coming out of conveyer.
5 out of 100 times, it is more than 10 minutes .
What is the process capability?
An
airlines recommends customer to give their food preference . Five
out of 200 cases, the passenger gets non veg when he ordered veg
What is the process capability?
Six
Sigma Methodology tells you how to calculate the Sigma Level of
such processes . Since sigma scale is applicable to every transaction
, it can be used in any area of business.
How to calculate Sigma Level
First
define Defects, Units and opportunities
Defects
Any
thing that causes customer dissatisfaction
Units
Any
thing that can be inspected for defects- it can be a finished
part or an assembly or sub assembly.
Example- a television set is a unit for final customer, but Printed
Circuit Board is a unit for the person who assembles TVs
Opportunities
The
possible defects in a product that may result in customer complaint
. Customer complaints are normally treated as irritants whereas
they should be treated as opportunities to correct . Hence the
usage opportunities.
Calculate DPU
Defects
Per Unit= Total Defective Units / Total Units Inspected
Calculate
DPMO
Defects
Per Million Opportunities = DPU x 1,000,000
Calculate
Sigma corresponding to the DPMO from Table 1
Summary
A
Six Sigma company is not a company that has to have all process
running at Six Sigma process level.
A six sigma
company is that company which has adopted six sigma strategy in
its business operations.
A six sigma
company is that company which has shifted from goal post mentality
to loss function mentality Six
Sigma strategy is a proven breakthrough technology that has a
vast reserve of tools and techniques If
these tools and techniques are applied wisely , they can make
a company prosperous.
Table
1
Number
of defects per million
possibilities of making an error |
Number
of defects per hundred
possibilities of making an error |
Associated
Sigma Levels |
66810 |
6.68 |
3.00 |
38950 |
3.89 |
3.25 |
22750 |
2.27 |
3.50 |
11870 |
1.18 |
3.75 |
6210 |
0.62 |
4.00 |
2890 |
0.28 |
4.25 |
1350 |
0.13 |
4.50 |
560 |
0.056 |
4.75 |
233 |
0.023 |
5.0 |
86 |
0.0086 |
5.25 |
32 |
0.0032 |
5.50 |
10.25 |
0.0010 |
5.75 |
3.4 |
0.00034 |
6.0 |
Exhibit
2
Process
Designation |
Process
Capability |
%
Output Out of Spec |
PPM
OUT OF SPEC |
1
Sigma |
.033 |
31.73 |
3,17,300 |
2
Sigma |
0.66 |
4.55 |
45,500 |
3
Sigma |
1.00 |
0.27 |
2700 |
4 Sigma |
1.33 |
0.0063 |
63 |
5
Sigma |
1.66 |
.0000057 |
0.57 |
6
Sigma |
2.00 |
0.0000002 |
0.002 |
Graphical
Representation of next slide |
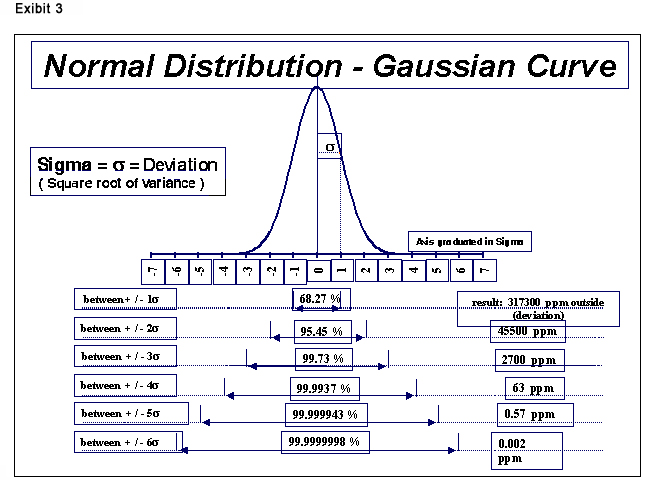
Exibit
4
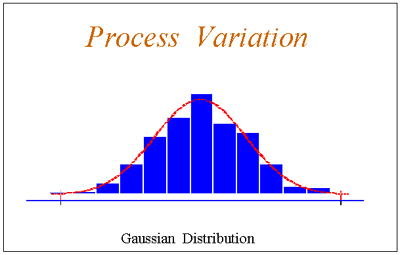
Exibit
5
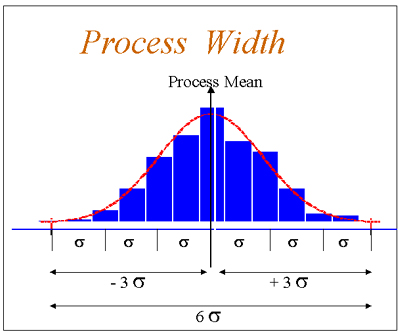
Exibit 6
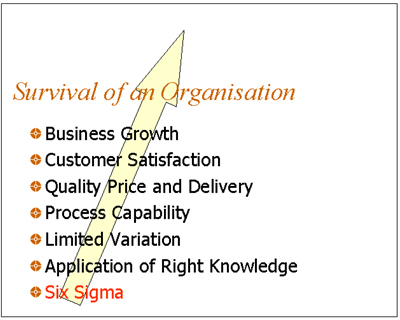
Exibit
7
|